Proper Cable Selection for Washdown Environments
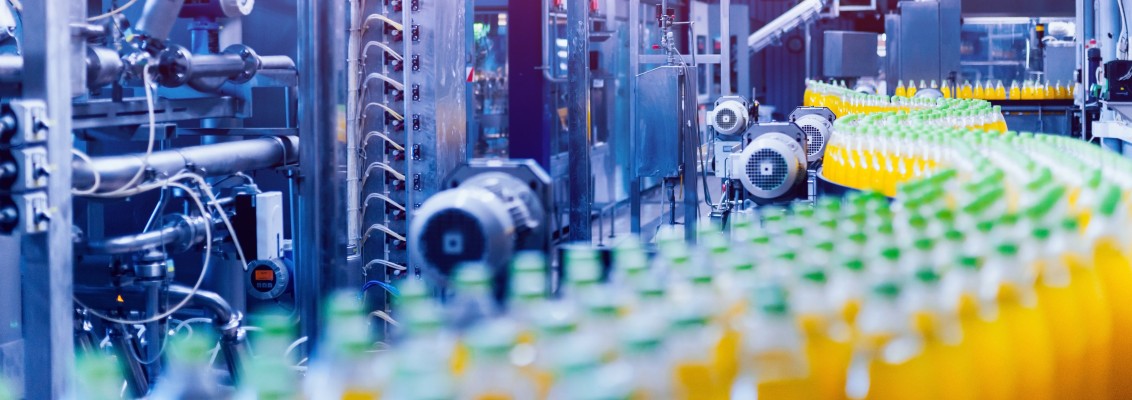
In the US, thousands of facilities are engaged in the supply of processed food and beverages, encompassing everything from poultry processing to soft drinks. These facilities employ well over a million workers and generate billions of dollars in annual sales.
Higher energy, raw material and feed costs, increased regulations implemented by government agencies (FDA, USDA, EPA and OSHA) and foreign competition — some from third-world countries lacking strict food safety regulations – are just a few of the challenges faced by today’s food and beverage producers. These hinderances to profitability can best be combated by reducing downtime.
All manufacturing plants experience downtime, whether it is scheduled or not. But, due to the perishable nature of the materials involved, the costs associated with downtime in a food and beverage plant can be very high. If power is lost during production, the current production batch may have to be scrapped. If a batch is contaminated, the result can be an expensive loss of man hours, raw materials and finished goods.
All industrial plants require a high sustainability level from their electrical cables, but most do not subject cables to high-pressure, washdown cleaning equipment that use high-temperature, caustic chemical solutions. Many experts estimate that washdown time in the food and beverage industry makes up between 20 and 30 percent of the overall production time. Due to the presence of heat, moisture and organic materials in food processing plants, cables and their enclosures are an ideal environment for bacteria, fungus and mold to grow on equipment. Stringent cleaning is a necessity in these facilities.
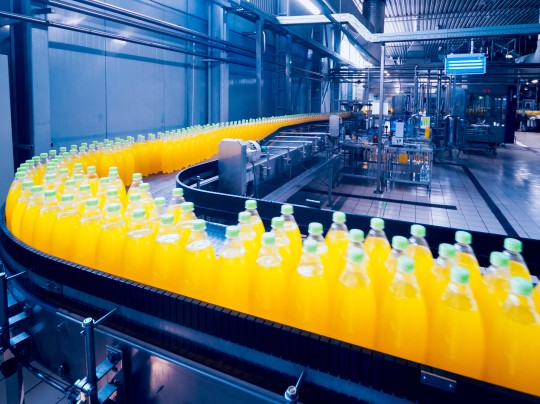
Washdown activity can shorten the life of the facility and equipment if proper components are not being used. For example, vinyl nylon tray cable (VNTC) is typically manufactured without fillers that ensure the cable’s concentricity.Therefore, VNTC cables tend to be convoluted, which makes a secure, sealed and water-tigh tfit with a cable gland impossible. This enables water and dust to become factors that can cause component failure. So, what cable is rugged enough to endure this unyielding environment while performing at an extremely high level?
For many years, HELUKABEL has been known for manufacturing a wide range of cables that provide reliable, efficient performance while being resistant to the range of chemical, thermal and physical stresses that lead to degradation.
In anticipation of increased demands for cables that are able to meet strict hygiene requirements, resist bacteria and fight contaminants, HELUKABEL had several different cable types tested in accordance with ECOLAB® test PM 40-1.
The cables were completely immersed in cleaning/disinfecting substances commonly used in the food and beverage industry for up to 28 days at constant room temperature. These chemicals include:
- Topactive 200 - Alkaline, chlorine-free foam cleaner
- Topactive 500 - Acid foam cleaning substance
- P3-topactive OKTO - Acid disinfectant based on peracetic acid/hydrogen peroxide
- P3-topax 66 - Alkaline foam cleaning detergent with active chlorine for machine cleaning
- P3-topax 990 - Neutral, non-oxidizing disinfecting agent for foam applications
- Distilled water - acts as a zero value
Upon completion, the test cables were then subjected to visual inspection to see if any swelling, brittleness or discoloring had occurred. HELUKABEL has tested and received the ECOLAB® seal of approval on 24 cable product families including command, control, servo, motor and feedback.
Control Cables with ECOLAB® Approval | VFD Cables with ECOLAB® Approval | Servo & Feedback Cables with ECOLAB® Approval |
PVC Insulation | XLPE Insulation | PP Insulation |
|
|
|
XLPE Insulation | ||
|
Some applications that require ECOLAB-approved cables are:
|
|
Along with needing ECOLAB® approvals, there are different types of cable jackets, and each provide different benefits for these difficult applications. The three main cable jackets are polyvinyl chloride (PVC), polyurethane (PUR) and thermoplastic elastomer (TPE). Each jacket type has different benefits like resistance to abrasion, washdown chemicals, or the mechanical stress associated with continuous-flexing applications. Finding the correct jacket type for your application can extend the life of the cable.
PVC is a popular general-purpose cable. It widely available, and typically has the best price point. PVC has a high moisture resistance, which makes it a good choice for washdown applications.
PUR is found mostly in Asia and Europe. This cable jacket type has good resistance against abrasion, oil and ozone. PUR is known for being halogen-free, and not containing chlorine, iodine, fluorine, bromine or astatine. This jacket type does have a limited temperature range compared to the other jacket types, typically -40°C to +80°C.
TPE is flexible, recyclable and has excellent cold temperature characteristics, usually -50°C to +125°C. This cable is resistant against aging in the sunlight, ozone and UV. TPE can withstand a high number of flexing cycles, typically around 10 million.
The table below details the jacket types and their resistance capabilities under different conditions and exposure to certain contaminants. Note that these relative ratings are based on average performance. Selective compounds can be specially added to the jacket material to improve its overall performance.
Resistance to | PVC | PUR | TPE |
Oxidation | Excellent | Excellent | Outstanding |
Heat | Good - Excellent | Excellent | Outstanding |
Oil | Fair | Outstanding | Outstanding |
Low-Temperature Flexibility | Poor - Good | Good | Good |
Weather, Sun | Good - Excellent | Excellent | Excellent |
Ozone | Excellent | Excellent | Excellent |
Abrasion | Fair - Good | Excellent | Good |
Electrical Properties | Excellent | Good | Excellent |
Flame | Excellent | Good | Outstanding |
Nuclear Radiation | Good | Good | Good |
Water | Good - Excellent | Good - Excellent | Excellent |
Acid | Good - Excellent | Good | Good |
Alkali | Good - Excellent | Excellent | Excellent |
Gasoline | Poor | Good | Excellent |
Benzol | Poor - Fair | Excellent | Excellent |
Degreaser Solvents | Poor - Fair | Excellent | Excellent |
Alcohol | Good - Excellent | Excellent | Excellent |
Weld Slag | Fair | Good | Good |
Choosing the right jacket type can help reduce failures in the field, the subsequent downtime and potential lost product, to reduce costs. If you have challenging applications in your canning, bottling, packaging or processing facility and need cable solutions that can withstand harsh conditions, HELUKABEL is the right choice for you. The high quality and reliability of our products guarantees peace of mind, making us a valued partner to many of the leading companies in the food & beverage industry around the world.
HELUKABEL has been the leading manufacturer of rugged cable solutions for the industrial sector — including the food and beverage space – since 1978. HELUKABEL will continue to develop cable products to help in the fight against contaminants in the food and beverage industry, and remain at the forefront of technological advancement.
Article Download
Click here to view this article in our digital download center.